ఇటీవలి సంవత్సరాలలో, కొత్త శక్తి పరిశ్రమ యొక్క వేగవంతమైన అభివృద్ధికి ధన్యవాదాలు, లేజర్ వెల్డింగ్ దాని వేగవంతమైన మరియు స్థిరమైన ప్రయోజనాల కారణంగా మొత్తం కొత్త శక్తి పరిశ్రమలోకి వేగంగా చొచ్చుకుపోయింది. వాటిలో, లేజర్ వెల్డింగ్ పరికరాలు మొత్తం కొత్త శక్తి పరిశ్రమలో అత్యధిక సంఖ్యలో అనువర్తనాలను కలిగి ఉన్నాయి.
లేజర్ వెల్డింగ్వేగవంతమైన వేగం, పెద్ద లోతు మరియు చిన్న వైకల్యం కారణంగా జీవితంలోని అన్ని రంగాలలో త్వరగా మొదటి ఎంపికగా మారింది. స్పాట్ వెల్డ్స్ నుండి బట్ వెల్డ్స్ వరకు, బిల్డ్-అప్ మరియు సీల్ వెల్డ్స్,లేజర్ వెల్డింగ్అసమానమైన ఖచ్చితత్వాన్ని మరియు నియంత్రణను అందిస్తుంది. సైనిక పరిశ్రమ, వైద్య సంరక్షణ, ఏరోస్పేస్, 3C ఆటో భాగాలు, మెకానికల్ షీట్ మెటల్, కొత్త శక్తి మరియు ఇతర పరిశ్రమలతో సహా పారిశ్రామిక ఉత్పత్తి మరియు తయారీలో ఇది ముఖ్యమైన పాత్ర పోషిస్తుంది.
ఇతర వెల్డింగ్ సాంకేతికతలతో పోలిస్తే, లేజర్ వెల్డింగ్ దాని ప్రత్యేక ప్రయోజనాలు మరియు అప్రయోజనాలు కలిగి ఉంది.
ప్రయోజనం:
1. వేగవంతమైన వేగం, పెద్ద లోతు మరియు చిన్న వైకల్యం.
2. వెల్డింగ్ సాధారణ ఉష్ణోగ్రత వద్ద లేదా ప్రత్యేక పరిస్థితుల్లో నిర్వహించబడుతుంది, మరియు వెల్డింగ్ పరికరాలు సులభం. ఉదాహరణకు, లేజర్ పుంజం విద్యుదయస్కాంత క్షేత్రంలో ప్రవహించదు. లేజర్లు వాక్యూమ్, గాలి లేదా నిర్దిష్ట వాయువు పరిసరాలలో వెల్డ్ చేయగలవు మరియు గాజు ద్వారా లేదా లేజర్ పుంజానికి పారదర్శకంగా ఉండే పదార్థాలను వెల్డ్ చేయగలవు.
3. ఇది టైటానియం మరియు క్వార్ట్జ్ వంటి వక్రీభవన పదార్థాలను వెల్డ్ చేయగలదు మరియు మంచి ఫలితాలతో అసమాన పదార్థాలను కూడా వెల్డ్ చేయగలదు.
4. లేజర్ ఫోకస్ చేసిన తర్వాత, పవర్ డెన్సిటీ ఎక్కువగా ఉంటుంది. కారక నిష్పత్తి 5:1కి చేరవచ్చు మరియు అధిక-శక్తి పరికరాలను వెల్డింగ్ చేసేటప్పుడు 10:1 వరకు చేరవచ్చు.
5. మైక్రో వెల్డింగ్ను నిర్వహించవచ్చు. లేజర్ పుంజం దృష్టి కేంద్రీకరించిన తర్వాత, ఒక చిన్న ప్రదేశాన్ని పొందవచ్చు మరియు ఖచ్చితంగా ఉంచవచ్చు. ఆటోమేటెడ్ మాస్ ఉత్పత్తిని సాధించడానికి మైక్రో మరియు చిన్న వర్క్పీస్ల అసెంబ్లీ మరియు వెల్డింగ్కు ఇది వర్తించవచ్చు.
6. ఇది హార్డ్-టు-రీచ్ ఏరియాలను వెల్డ్ చేయగలదు మరియు గొప్ప సౌలభ్యంతో నాన్-కాంటాక్ట్ సుదూర వెల్డింగ్ చేయగలదు. ముఖ్యంగా ఇటీవలి సంవత్సరాలలో, YAG లేజర్ ప్రాసెసింగ్ టెక్నాలజీ ఆప్టికల్ ఫైబర్ ట్రాన్స్మిషన్ టెక్నాలజీని స్వీకరించింది, ఇది లేజర్ వెల్డింగ్ టెక్నాలజీని మరింత విస్తృతంగా ప్రచారం చేయడానికి మరియు వర్తింపజేయడానికి వీలు కల్పించింది.
7. లేజర్ పుంజం సమయం మరియు ప్రదేశంలో విభజించడం సులభం, మరియు బహుళ కిరణాలు ఏకకాలంలో బహుళ ప్రదేశాలలో ప్రాసెస్ చేయబడతాయి, మరింత ఖచ్చితమైన వెల్డింగ్ కోసం పరిస్థితులను అందిస్తాయి.
లోపం:
1. వర్క్పీస్ యొక్క అసెంబ్లీ ఖచ్చితత్వం ఎక్కువగా ఉండాలి మరియు వర్క్పీస్పై పుంజం యొక్క స్థానం గణనీయంగా విచలనం చేయబడదు. ఎందుకంటే ఫోకస్ చేసిన తర్వాత లేజర్ స్పాట్ పరిమాణం చిన్నది మరియు వెల్డ్ సీమ్ ఇరుకైనది, పూరక మెటల్ పదార్థాలను జోడించడం కష్టతరం చేస్తుంది. వర్క్పీస్ యొక్క అసెంబ్లీ ఖచ్చితత్వం లేదా పుంజం యొక్క స్థాన ఖచ్చితత్వం అవసరాలను తీర్చకపోతే, వెల్డింగ్ లోపాలు సంభవించే అవకాశం ఉంది.
2. లేజర్లు మరియు సంబంధిత వ్యవస్థల ధర ఎక్కువగా ఉంటుంది మరియు ఒక-సమయం పెట్టుబడి పెద్దది.
సాధారణ లేజర్ వెల్డింగ్ లోపాలులిథియం బ్యాటరీ తయారీలో
1. వెల్డింగ్ సచ్ఛిద్రత
లో సాధారణ లోపాలులేజర్ వెల్డింగ్రంధ్రాలు ఉంటాయి. వెల్డింగ్ కరిగిన పూల్ లోతైన మరియు ఇరుకైనది. లేజర్ వెల్డింగ్ ప్రక్రియలో, నైట్రోజన్ బయటి నుండి కరిగిన కొలనుపై దాడి చేస్తుంది. లోహం యొక్క శీతలీకరణ మరియు ఘనీభవన ప్రక్రియలో, నత్రజని యొక్క ద్రావణీయత ఉష్ణోగ్రత తగ్గడంతో తగ్గుతుంది. కరిగిన పూల్ లోహం స్ఫటికీకరించడం ప్రారంభించినప్పుడు చల్లబడినప్పుడు, ద్రావణీయత తీవ్రంగా మరియు అకస్మాత్తుగా పడిపోతుంది. ఈ సమయంలో, పెద్ద మొత్తంలో వాయువు బుడగలు ఏర్పడటానికి అవక్షేపించబడుతుంది. బుడగలు తేలియాడే వేగం మెటల్ స్ఫటికీకరణ వేగం కంటే తక్కువగా ఉంటే, రంధ్రాలు ఉత్పత్తి అవుతాయి.
లిథియం బ్యాటరీ పరిశ్రమలోని అనువర్తనాల్లో, సానుకూల ఎలక్ట్రోడ్ యొక్క వెల్డింగ్ సమయంలో రంధ్రాలు ముఖ్యంగా సంభవించే అవకాశం ఉందని మేము తరచుగా కనుగొంటాము, అయితే ప్రతికూల ఎలక్ట్రోడ్ యొక్క వెల్డింగ్ సమయంలో చాలా అరుదుగా సంభవిస్తుంది. ఎందుకంటే పాజిటివ్ ఎలక్ట్రోడ్ అల్యూమినియంతోనూ, నెగిటివ్ ఎలక్ట్రోడ్ రాగితోనూ తయారవుతుంది. వెల్డింగ్ సమయంలో, ఉపరితలంపై ఉన్న ద్రవ అల్యూమినియం అంతర్గత వాయువు పూర్తిగా పొంగిపొర్లడానికి ముందు ఘనీభవిస్తుంది, గ్యాస్ పొంగిపోకుండా మరియు పెద్ద మరియు చిన్న రంధ్రాలను ఏర్పరుస్తుంది. చిన్న స్టోమాటా.
పైన పేర్కొన్న రంధ్రాల కారణాలతో పాటు, రంధ్రాలలో బయటి గాలి, తేమ, ఉపరితల చమురు మొదలైనవి కూడా ఉంటాయి. అదనంగా, నత్రజని ఊదడం యొక్క దిశ మరియు కోణం కూడా రంధ్రాల ఏర్పడటాన్ని ప్రభావితం చేస్తుంది.
వెల్డింగ్ రంధ్రాల సంభవనీయతను ఎలా తగ్గించాలి?
మొదట, ముందువెల్డింగ్, ఇన్కమింగ్ పదార్థాల ఉపరితలంపై చమురు మరకలు మరియు మలినాలను సమయం లో శుభ్రం చేయాలి; లిథియం బ్యాటరీల ఉత్పత్తిలో, ఇన్కమింగ్ మెటీరియల్ తనిఖీ అనేది ఒక ముఖ్యమైన ప్రక్రియ.
రెండవది, షీల్డింగ్ గ్యాస్ ప్రవాహాన్ని వెల్డింగ్ వేగం, శక్తి, స్థానం మొదలైన అంశాల ప్రకారం సర్దుబాటు చేయాలి మరియు చాలా పెద్దది లేదా చాలా చిన్నది కాదు. లేజర్ పవర్ మరియు ఫోకస్ పొజిషన్ వంటి కారకాలకు అనుగుణంగా రక్షిత క్లోక్ ప్రెజర్ సర్దుబాటు చేయబడాలి మరియు చాలా ఎక్కువగా లేదా చాలా తక్కువగా ఉండకూడదు. రక్షిత క్లోక్ నాజిల్ యొక్క ఆకృతిని ఆకారం, దిశ మరియు వెల్డ్ యొక్క ఇతర కారకాలకు అనుగుణంగా సర్దుబాటు చేయాలి, తద్వారా రక్షిత వస్త్రం వెల్డింగ్ ప్రాంతాన్ని సమానంగా కవర్ చేస్తుంది.
మూడవది, వర్క్షాప్లో గాలిలో ఉష్ణోగ్రత, తేమ మరియు ధూళిని నియంత్రించండి. పరిసర ఉష్ణోగ్రత మరియు తేమ ఉపరితలం మరియు రక్షిత వాయువు యొక్క ఉపరితలంపై తేమను ప్రభావితం చేస్తుంది, ఇది కరిగిన కొలనులో నీటి ఆవిరి ఉత్పత్తి మరియు తప్పించుకోవడాన్ని ప్రభావితం చేస్తుంది. పరిసర ఉష్ణోగ్రత మరియు తేమ చాలా ఎక్కువగా ఉంటే, ఉపరితలం మరియు రక్షిత వాయువు యొక్క ఉపరితలంపై చాలా తేమ ఉంటుంది, ఇది పెద్ద మొత్తంలో నీటి ఆవిరిని ఉత్పత్తి చేస్తుంది, ఫలితంగా రంధ్రాలు ఏర్పడతాయి. పరిసర ఉష్ణోగ్రత మరియు తేమ చాలా తక్కువగా ఉంటే, ఉపరితల ఉపరితలంపై మరియు రక్షిత వాయువులో చాలా తక్కువ తేమ ఉంటుంది, నీటి ఆవిరి ఉత్పత్తిని తగ్గిస్తుంది, తద్వారా రంధ్రాలను తగ్గిస్తుంది; నాణ్యమైన సిబ్బంది వెల్డింగ్ స్టేషన్లో ఉష్ణోగ్రత, తేమ మరియు ధూళి యొక్క లక్ష్య విలువను గుర్తించనివ్వండి.
నాల్గవది, లేజర్ డీప్ పెనెట్రేషన్ వెల్డింగ్లో రంధ్రాలను తగ్గించడానికి లేదా తొలగించడానికి బీమ్ స్వింగ్ పద్ధతి ఉపయోగించబడుతుంది. వెల్డింగ్ సమయంలో స్వింగ్ జోడించడం వలన, వెల్డ్ సీమ్కు పుంజం యొక్క రెసిప్రొకేటింగ్ స్వింగ్ వెల్డ్ సీమ్ యొక్క భాగాన్ని పునరావృతం చేయడానికి కారణమవుతుంది, ఇది వెల్డింగ్ పూల్లో ద్రవ మెటల్ యొక్క నివాస సమయాన్ని పొడిగిస్తుంది. అదే సమయంలో, పుంజం యొక్క విక్షేపం యూనిట్ ప్రాంతానికి ఉష్ణ ఇన్పుట్ను కూడా పెంచుతుంది. వెల్డ్ యొక్క లోతు-వెడల్పు నిష్పత్తి తగ్గిపోతుంది, ఇది బుడగలు యొక్క ఆవిర్భావానికి అనుకూలంగా ఉంటుంది, తద్వారా రంధ్రాలను తొలగిస్తుంది. మరోవైపు, పుంజం యొక్క స్వింగ్ చిన్న రంధ్రం తదనుగుణంగా స్వింగ్ చేయడానికి కారణమవుతుంది, ఇది వెల్డింగ్ పూల్ కోసం కదిలించే శక్తిని కూడా అందిస్తుంది, వెల్డింగ్ పూల్ యొక్క ఉష్ణప్రసరణ మరియు గందరగోళాన్ని పెంచుతుంది మరియు రంధ్రాలను తొలగించడంలో ప్రయోజనకరమైన ప్రభావాన్ని కలిగి ఉంటుంది.
ఐదవది, పల్స్ ఫ్రీక్వెన్సీ, పల్స్ ఫ్రీక్వెన్సీ అనేది యూనిట్ సమయానికి లేజర్ పుంజం ద్వారా విడుదలయ్యే పప్పుల సంఖ్యను సూచిస్తుంది, ఇది కరిగిన పూల్లో వేడి ఇన్పుట్ మరియు వేడి చేరడంపై ప్రభావం చూపుతుంది, ఆపై కరిగిన ఉష్ణోగ్రత క్షేత్రం మరియు ప్రవాహ క్షేత్రాన్ని ప్రభావితం చేస్తుంది. కొలను. పల్స్ ఫ్రీక్వెన్సీ చాలా ఎక్కువగా ఉంటే, అది కరిగిన పూల్లో అధిక ఉష్ణ ఇన్పుట్కు దారి తీస్తుంది, దీని వలన కరిగిన పూల్ యొక్క ఉష్ణోగ్రత చాలా ఎక్కువగా ఉంటుంది, లోహ ఆవిరి లేదా ఇతర మూలకాలను అధిక ఉష్ణోగ్రతల వద్ద అస్థిరంగా ఉత్పత్తి చేస్తుంది, ఫలితంగా రంధ్రాలు ఏర్పడతాయి. పల్స్ ఫ్రీక్వెన్సీ చాలా తక్కువగా ఉంటే, అది కరిగిన పూల్లో తగినంత వేడిని చేరడానికి దారి తీస్తుంది, దీని వలన కరిగిన పూల్ యొక్క ఉష్ణోగ్రత చాలా తక్కువగా ఉంటుంది, దీని వలన గ్యాస్ కరిగిపోవడం మరియు తప్పించుకోవడం తగ్గుతుంది, ఫలితంగా రంధ్రాల ఏర్పడతాయి. సాధారణంగా చెప్పాలంటే, పల్స్ ఫ్రీక్వెన్సీని సబ్స్ట్రేట్ మందం మరియు లేజర్ పవర్ ఆధారంగా సహేతుకమైన పరిధిలో ఎంచుకోవాలి మరియు చాలా ఎక్కువ లేదా చాలా తక్కువగా ఉండకూడదు.
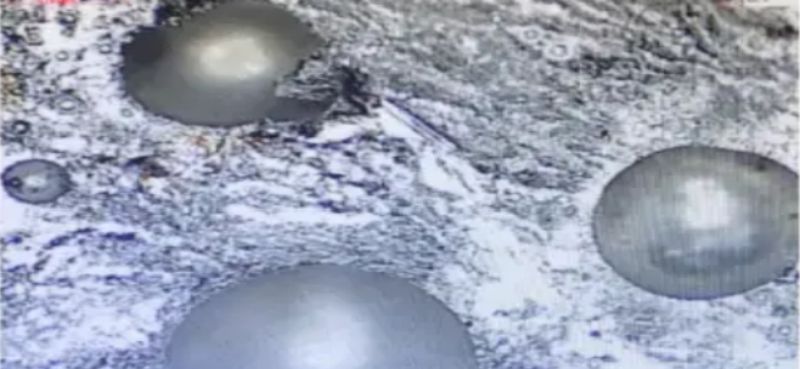
వెల్డింగ్ రంధ్రాలు (లేజర్ వెల్డింగ్)
2. వెల్డ్ స్పాటర్
వెల్డింగ్ ప్రక్రియలో ఉత్పన్నమయ్యే చిందులు, లేజర్ వెల్డింగ్ అనేది వెల్డ్ యొక్క ఉపరితల నాణ్యతను తీవ్రంగా ప్రభావితం చేస్తుంది మరియు లెన్స్ను కలుషితం చేస్తుంది మరియు దెబ్బతీస్తుంది. సాధారణ పనితీరు క్రింది విధంగా ఉంటుంది: లేజర్ వెల్డింగ్ పూర్తయిన తర్వాత, అనేక మెటల్ కణాలు పదార్థం లేదా వర్క్పీస్ యొక్క ఉపరితలంపై కనిపిస్తాయి మరియు పదార్థం లేదా వర్క్పీస్ యొక్క ఉపరితలంపై కట్టుబడి ఉంటాయి. అత్యంత సహజమైన పనితీరు ఏమిటంటే, గాల్వనోమీటర్ యొక్క మోడ్లో వెల్డింగ్ చేసినప్పుడు, గాల్వనోమీటర్ యొక్క రక్షిత లెన్స్ ఉపయోగించిన కాలం తర్వాత, ఉపరితలంపై దట్టమైన గుంటలు ఉంటాయి మరియు ఈ గుంటలు వెల్డింగ్ స్పేటర్ వల్ల ఏర్పడతాయి. చాలా కాలం తర్వాత, కాంతిని నిరోధించడం సులభం, మరియు వెల్డింగ్ లైట్తో సమస్యలు ఉంటాయి, ఫలితంగా విరిగిన వెల్డింగ్ మరియు వర్చువల్ వెల్డింగ్ వంటి సమస్యల శ్రేణి ఏర్పడుతుంది.
స్ప్లాషింగ్ యొక్క కారణాలు ఏమిటి?
మొదటిది, శక్తి సాంద్రత, ఎక్కువ శక్తి సాంద్రత, చిమ్మటను ఉత్పత్తి చేయడం సులభం, మరియు చిమ్ము నేరుగా శక్తి సాంద్రతకు సంబంధించినది. ఇది శతాబ్దాల నాటి సమస్య. కనీసం ఇప్పటి వరకు పరిశ్రమలో చిందులు తొక్కే సమస్యను పరిష్కరించలేక పోయిందని, కాస్త తగ్గిందని చెప్పొచ్చు. లిథియం బ్యాటరీ పరిశ్రమలో, స్ప్లాషింగ్ అనేది బ్యాటరీ షార్ట్ సర్క్యూట్కు అతిపెద్ద అపరాధి, కానీ అది మూల కారణాన్ని పరిష్కరించలేకపోయింది. బ్యాటరీపై చిందుల ప్రభావం రక్షణ కోణం నుండి మాత్రమే తగ్గించబడుతుంది. ఉదాహరణకు, వెల్డింగ్ భాగం చుట్టూ ధూళిని తొలగించే పోర్ట్లు మరియు రక్షిత కవర్ల సర్కిల్ జోడించబడతాయి మరియు చిందుల ప్రభావం లేదా బ్యాటరీకి నష్టం జరగకుండా నిరోధించడానికి ఎయిర్ కత్తుల వరుసలు సర్కిల్లలో జోడించబడతాయి. వెల్డింగ్ స్టేషన్ చుట్టూ పర్యావరణం, ఉత్పత్తులు మరియు భాగాలను నాశనం చేయడం అంటే అయిపోయిందని చెప్పవచ్చు.
స్పేటర్ సమస్యను పరిష్కరించడానికి, వెల్డింగ్ శక్తిని తగ్గించడం చిమ్మటను తగ్గించడంలో సహాయపడుతుందని మాత్రమే చెప్పవచ్చు. వ్యాప్తి సరిపోకపోతే వెల్డింగ్ వేగాన్ని తగ్గించడం కూడా సహాయపడుతుంది. కానీ కొన్ని ప్రత్యేక ప్రక్రియ అవసరాలలో, ఇది తక్కువ ప్రభావాన్ని కలిగి ఉంటుంది. ఇది అదే ప్రక్రియ, వివిధ యంత్రాలు మరియు పదార్థాల వివిధ బ్యాచ్లు పూర్తిగా వేర్వేరు వెల్డింగ్ ప్రభావాలను కలిగి ఉంటాయి. అందువల్ల, కొత్త శక్తి పరిశ్రమలో ఒక అలిఖిత నియమం ఉంది, ఒక పరికరం కోసం వెల్డింగ్ పారామితుల యొక్క ఒక సెట్.
రెండవది, ప్రాసెస్ చేయబడిన పదార్థం లేదా వర్క్పీస్ యొక్క ఉపరితలం శుభ్రం చేయకపోతే, చమురు మరకలు లేదా కాలుష్య కారకాలు కూడా తీవ్రమైన స్ప్లాష్లకు కారణమవుతాయి. ఈ సమయంలో, ప్రాసెస్ చేయబడిన పదార్థం యొక్క ఉపరితలం శుభ్రం చేయడం సులభమయిన విషయం.
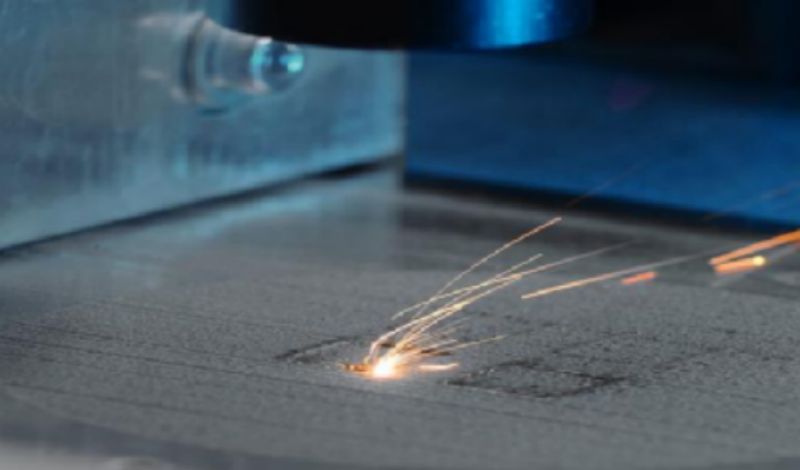
3. లేజర్ వెల్డింగ్ యొక్క అధిక ప్రతిబింబం
సాధారణంగా చెప్పాలంటే, అధిక ప్రతిబింబం అనేది ప్రాసెసింగ్ మెటీరియల్ ఒక చిన్న రెసిస్టివిటీ, సాపేక్షంగా మృదువైన ఉపరితలం మరియు సమీప-ఇన్ఫ్రారెడ్ లేజర్లకు తక్కువ శోషణ రేటును కలిగి ఉంటుంది, ఇది పెద్ద మొత్తంలో లేజర్ ఉద్గారాలకు దారితీస్తుంది మరియు చాలా లేజర్లు ఉపయోగించబడుతున్నాయి. నిలువుగా ఉన్న పదార్థం లేదా తక్కువ మొత్తంలో వంపు కారణంగా, తిరిగి వచ్చే లేజర్ కాంతి అవుట్పుట్ హెడ్లోకి తిరిగి ప్రవేశిస్తుంది మరియు తిరిగి వచ్చే కాంతిలో కొంత భాగాన్ని కూడా శక్తి-ప్రసార ఫైబర్తో కలుపుతారు మరియు ఫైబర్తో పాటు లోపలికి తిరిగి ప్రసారం చేయబడుతుంది. లేజర్ యొక్క, లేజర్ లోపల ప్రధాన భాగాలు అధిక ఉష్ణోగ్రత వద్ద కొనసాగేలా చేస్తుంది.
లేజర్ వెల్డింగ్ సమయంలో ప్రతిబింబం చాలా ఎక్కువగా ఉన్నప్పుడు, క్రింది పరిష్కారాలను తీసుకోవచ్చు:
3.1 యాంటీ-రిఫ్లెక్షన్ కోటింగ్ను ఉపయోగించండి లేదా పదార్థం యొక్క ఉపరితలంపై చికిత్స చేయండి: వెల్డింగ్ పదార్థం యొక్క ఉపరితలంపై యాంటీ-రిఫ్లెక్షన్ పూతతో పూత పూయడం వల్ల లేజర్ యొక్క పరావర్తనను సమర్థవంతంగా తగ్గిస్తుంది. ఈ పూత సాధారణంగా తక్కువ పరావర్తనం కలిగిన ప్రత్యేక ఆప్టికల్ పదార్థం, ఇది తిరిగి ప్రతిబింబించే బదులు లేజర్ శక్తిని గ్రహిస్తుంది. ప్రస్తుత కలెక్టర్ వెల్డింగ్, సాఫ్ట్ కనెక్షన్ మొదలైన కొన్ని ప్రక్రియలలో, ఉపరితలం కూడా చిత్రించబడవచ్చు.
3.2 వెల్డింగ్ కోణాన్ని సర్దుబాటు చేయండి: వెల్డింగ్ కోణాన్ని సర్దుబాటు చేయడం ద్వారా, లేజర్ పుంజం వెల్డింగ్ మెటీరియల్పై మరింత సరైన కోణంలో సంభవించవచ్చు మరియు ప్రతిబింబం సంభవించడాన్ని తగ్గిస్తుంది. సాధారణంగా, వెల్డింగ్ చేయవలసిన పదార్థం యొక్క ఉపరితలంపై లంబంగా లేజర్ పుంజం సంఘటనను కలిగి ఉండటం ప్రతిబింబాలను తగ్గించడానికి మంచి మార్గం.
3.3 సహాయక శోషక పదార్థాన్ని జోడించడం: వెల్డింగ్ ప్రక్రియలో, పొడి లేదా ద్రవ వంటి సహాయక శోషక యొక్క నిర్దిష్ట మొత్తం వెల్డ్కు జోడించబడుతుంది. ఈ శోషకాలు లేజర్ శక్తిని గ్రహిస్తాయి మరియు ప్రతిబింబాన్ని తగ్గిస్తాయి. నిర్దిష్ట వెల్డింగ్ పదార్థాలు మరియు అప్లికేషన్ దృశ్యాల ఆధారంగా తగిన శోషకాన్ని ఎంచుకోవాలి. లిథియం బ్యాటరీ పరిశ్రమలో, ఇది అసంభవం.
3.4 లేజర్ను ప్రసారం చేయడానికి ఆప్టికల్ ఫైబర్ని ఉపయోగించండి: వీలైతే, పరావర్తనాన్ని తగ్గించడానికి వెల్డింగ్ స్థానానికి లేజర్ను ప్రసారం చేయడానికి ఆప్టికల్ ఫైబర్ను ఉపయోగించవచ్చు. ఆప్టికల్ ఫైబర్స్ వెల్డింగ్ మెటీరియల్ యొక్క ఉపరితలంపై ప్రత్యక్షంగా బహిర్గతం కాకుండా మరియు ప్రతిబింబాల సంభవనీయతను తగ్గించడానికి వెల్డింగ్ ప్రాంతానికి లేజర్ పుంజాన్ని మార్గనిర్దేశం చేయగలవు.
3.5 లేజర్ పారామితులను సర్దుబాటు చేయడం: లేజర్ శక్తి, ఫోకల్ పొడవు మరియు ఫోకల్ వ్యాసం వంటి పారామితులను సర్దుబాటు చేయడం ద్వారా, లేజర్ శక్తి పంపిణీని నియంత్రించవచ్చు మరియు ప్రతిబింబాలను తగ్గించవచ్చు. కొన్ని రిఫ్లెక్టివ్ మెటీరియల్స్ కోసం, లేజర్ శక్తిని తగ్గించడం అనేది ప్రతిబింబాలను తగ్గించడానికి ఒక ప్రభావవంతమైన మార్గం.
3.6 బీమ్ స్ప్లిటర్ను ఉపయోగించండి: బీమ్ స్ప్లిటర్ లేజర్ శక్తిలో కొంత భాగాన్ని శోషణ పరికరంలోకి మార్గనిర్దేశం చేస్తుంది, తద్వారా ప్రతిబింబాల సంభవనీయతను తగ్గిస్తుంది. బీమ్ స్ప్లిటింగ్ పరికరాలు సాధారణంగా ఆప్టికల్ భాగాలు మరియు శోషకాలను కలిగి ఉంటాయి మరియు తగిన భాగాలను ఎంచుకోవడం మరియు పరికరం యొక్క లేఅవుట్ను సర్దుబాటు చేయడం ద్వారా, తక్కువ పరావర్తనను సాధించవచ్చు.
4. వెల్డింగ్ అండర్కట్
లిథియం బ్యాటరీ తయారీ ప్రక్రియలో, ఏ ప్రక్రియలు అండర్కటింగ్కు కారణమవుతాయి? అండర్కటింగ్ ఎందుకు జరుగుతుంది? దానిని విశ్లేషిద్దాం.
అండర్కట్, సాధారణంగా వెల్డింగ్ ముడి పదార్థాలు ఒకదానితో ఒకటి బాగా కలపబడవు, గ్యాప్ చాలా పెద్దది లేదా గాడి కనిపిస్తుంది, లోతు మరియు వెడల్పు ప్రాథమికంగా 0.5 మిమీ కంటే ఎక్కువగా ఉంటుంది, మొత్తం పొడవు వెల్డ్ పొడవులో 10% కంటే ఎక్కువగా ఉంటుంది లేదా ఉత్పత్తి ప్రక్రియ ప్రమాణం కంటే అభ్యర్థించిన పొడవు కంటే ఎక్కువ.
మొత్తం లిథియం బ్యాటరీ తయారీ ప్రక్రియలో, అండర్కటింగ్ జరిగే అవకాశం ఉంది మరియు ఇది సాధారణంగా సీలింగ్ ప్రీ-వెల్డింగ్ మరియు స్థూపాకార కవర్ ప్లేట్ యొక్క వెల్డింగ్ మరియు స్క్వేర్ అల్యూమినియం షెల్ కవర్ ప్లేట్ యొక్క సీలింగ్ ప్రీ-వెల్డింగ్ మరియు వెల్డింగ్లో పంపిణీ చేయబడుతుంది. ప్రధాన కారణం ఏమిటంటే, సీలింగ్ కవర్ ప్లేట్ షెల్తో వెల్డింగ్కి సహకరించాలి, సీలింగ్ కవర్ ప్లేట్ మరియు షెల్ మధ్య మ్యాచింగ్ ప్రక్రియ అధిక వెల్డ్ గ్యాప్లు, గ్రూవ్లు, కూలిపోవడం మొదలైన వాటికి అవకాశం ఉంది, కాబట్టి ఇది ముఖ్యంగా అండర్కట్లకు గురవుతుంది. .
కాబట్టి అండర్కటింగ్కు కారణమేమిటి?
వెల్డింగ్ వేగం చాలా వేగంగా ఉంటే, వెల్డ్ మధ్యలో ఉన్న చిన్న రంధ్రం వెనుక ఉన్న ద్రవ మెటల్ పునఃపంపిణీ చేయడానికి సమయం ఉండదు, దీని ఫలితంగా వెల్డ్ యొక్క రెండు వైపులా ఘనీభవనం మరియు అండర్కటింగ్ జరుగుతుంది. పై పరిస్థితి దృష్ట్యా, మేము వెల్డింగ్ పారామితులను ఆప్టిమైజ్ చేయాలి. సరళంగా చెప్పాలంటే, ఇది వివిధ పారామితులను ధృవీకరించడానికి పునరావృత ప్రయోగాలు మరియు తగిన పారామితులు కనుగొనబడే వరకు DOE చేస్తూనే ఉంటుంది.
2. మితిమీరిన వెల్డ్ ఖాళీలు, పొడవైన కమ్మీలు, కూలిపోవడం మొదలైనవి వెల్డింగ్ పదార్థాల కరిగిన లోహాన్ని ఖాళీలను పూరించడాన్ని తగ్గిస్తాయి, తద్వారా అండర్కట్లు సంభవించే అవకాశం ఉంది. ఇది పరికరాలు మరియు ముడి పదార్థాల ప్రశ్న. వెల్డింగ్ ముడి పదార్థాలు మా ప్రక్రియ యొక్క ఇన్కమింగ్ మెటీరియల్ అవసరాలను తీరుస్తున్నాయా, పరికరాల ఖచ్చితత్వం అవసరాలకు అనుగుణంగా ఉందా, మొదలైనవి. సాధారణ అభ్యాసం సరఫరాదారులను మరియు పరికరాలకు బాధ్యత వహించే వ్యక్తులను నిరంతరం హింసించడం మరియు కొట్టడం.
3. లేజర్ వెల్డింగ్ ముగింపులో శక్తి చాలా వేగంగా పడిపోతే, చిన్న రంధ్రం కూలిపోవచ్చు, ఫలితంగా స్థానిక అండర్కటింగ్ ఏర్పడుతుంది. శక్తి మరియు వేగం యొక్క సరైన సరిపోలిక అండర్కట్స్ ఏర్పడకుండా సమర్థవంతంగా నిరోధించవచ్చు. పాత సామెత ప్రకారం, ప్రయోగాలను పునరావృతం చేయండి, వివిధ పారామితులను ధృవీకరించండి మరియు మీరు సరైన పారామితులను కనుగొనే వరకు DOEని కొనసాగించండి.
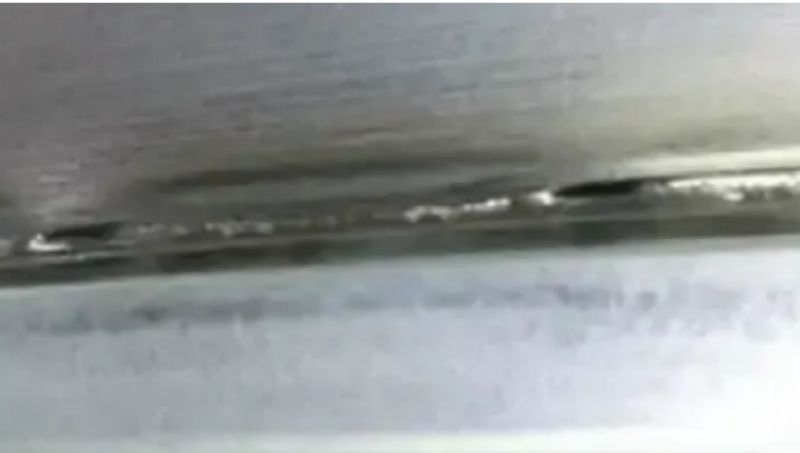
5. వెల్డ్ సెంటర్ పతనం
వెల్డింగ్ వేగం నెమ్మదిగా ఉంటే, కరిగిన పూల్ పెద్దదిగా మరియు విశాలంగా ఉంటుంది, కరిగిన మెటల్ మొత్తం పెరుగుతుంది. ఇది ఉపరితల ఉద్రిక్తతను నిర్వహించడం కష్టతరం చేస్తుంది. కరిగిన లోహం చాలా బరువుగా మారినప్పుడు, వెల్డ్ యొక్క మధ్యభాగం మునిగిపోతుంది మరియు డిప్స్ మరియు గుంటలు ఏర్పడవచ్చు. ఈ సందర్భంలో, మెల్ట్ పూల్ కూలిపోకుండా నిరోధించడానికి శక్తి సాంద్రతను తగిన విధంగా తగ్గించాల్సిన అవసరం ఉంది.
మరొక పరిస్థితిలో, వెల్డింగ్ గ్యాప్ కేవలం చిల్లులు కలిగించకుండా పతనాన్ని ఏర్పరుస్తుంది. ఇది నిస్సందేహంగా పరికరాలు ప్రెస్ ఫిట్ సమస్య.
లేజర్ వెల్డింగ్ సమయంలో సంభవించే లోపాలు మరియు వివిధ లోపాల కారణాలపై సరైన అవగాహన ఏదైనా అసాధారణమైన వెల్డింగ్ సమస్యలను పరిష్కరించడానికి మరింత లక్ష్య విధానాన్ని అనుమతిస్తుంది.
6. వెల్డ్ పగుళ్లు
నిరంతర లేజర్ వెల్డింగ్ సమయంలో కనిపించే పగుళ్లు ప్రధానంగా ఉష్ణ పగుళ్లు, క్రిస్టల్ పగుళ్లు మరియు ద్రవీకరణ పగుళ్లు వంటివి. ఈ పగుళ్లకు ప్రధాన కారణం వెల్డ్ పూర్తిగా పటిష్టం కావడానికి ముందు ఉత్పత్తి చేయబడిన పెద్ద సంకోచం.
లేజర్ వెల్డింగ్లో పగుళ్లు ఏర్పడటానికి క్రింది కారణాలు కూడా ఉన్నాయి:
1. అసమంజసమైన వెల్డ్ డిజైన్: వెల్డ్ యొక్క జ్యామితి మరియు పరిమాణం యొక్క సరికాని డిజైన్ వెల్డింగ్ ఒత్తిడి ఏకాగ్రతకు కారణం కావచ్చు, తద్వారా పగుళ్లు ఏర్పడవచ్చు. వెల్డింగ్ ఒత్తిడి ఏకాగ్రతను నివారించడానికి వెల్డ్ డిజైన్ను ఆప్టిమైజ్ చేయడం పరిష్కారం. మీరు తగిన ఆఫ్సెట్ వెల్డ్స్ను ఉపయోగించవచ్చు, వెల్డ్ ఆకారాన్ని మార్చవచ్చు, మొదలైనవి.
2. వెల్డింగ్ పారామితుల అసమతుల్యత: చాలా వేగవంతమైన వెల్డింగ్ వేగం, చాలా అధిక శక్తి మొదలైనవి వంటి వెల్డింగ్ పారామితుల యొక్క సరికాని ఎంపిక, వెల్డింగ్ ప్రాంతంలో అసమాన ఉష్ణోగ్రత మార్పులకు దారితీయవచ్చు, ఫలితంగా పెద్ద వెల్డింగ్ ఒత్తిడి మరియు పగుళ్లు ఏర్పడతాయి. నిర్దిష్ట పదార్థం మరియు వెల్డింగ్ పరిస్థితులకు సరిపోయేలా వెల్డింగ్ పారామితులను సర్దుబాటు చేయడం పరిష్కారం.
3. వెల్డింగ్ ఉపరితలం యొక్క పేలవమైన తయారీ: ఆక్సైడ్లు, గ్రీజు మొదలైన వాటిని తొలగించడం వంటి వెల్డింగ్ ఉపరితలాన్ని సరిగ్గా శుభ్రపరచడం మరియు ముందుగా చికిత్స చేయడంలో వైఫల్యం, వెల్డ్ యొక్క నాణ్యత మరియు బలాన్ని ప్రభావితం చేస్తుంది మరియు సులభంగా పగుళ్లకు దారి తీస్తుంది. వెల్డింగ్ ప్రాంతంలోని మలినాలను మరియు కలుషితాలు సమర్థవంతంగా చికిత్స చేయబడతాయని నిర్ధారించడానికి వెల్డింగ్ ఉపరితలాన్ని తగినంతగా శుభ్రపరచడం మరియు ముందుగా చికిత్స చేయడం పరిష్కారం.
4. వెల్డింగ్ హీట్ ఇన్పుట్ యొక్క సరికాని నియంత్రణ: వెల్డింగ్ సమయంలో అధిక ఉష్ణోగ్రత, వెల్డింగ్ పొర యొక్క సరికాని శీతలీకరణ రేటు మొదలైన వెల్డింగ్ సమయంలో హీట్ ఇన్పుట్ యొక్క పేలవమైన నియంత్రణ, వెల్డింగ్ ప్రాంతం యొక్క నిర్మాణంలో మార్పులకు దారి తీస్తుంది, ఫలితంగా పగుళ్లు ఏర్పడతాయి. . వేడెక్కడం మరియు వేగవంతమైన శీతలీకరణను నివారించడానికి వెల్డింగ్ సమయంలో ఉష్ణోగ్రత మరియు శీతలీకరణ రేటును నియంత్రించడం పరిష్కారం.
5. తగినంత ఒత్తిడి ఉపశమనం: వెల్డింగ్ తర్వాత తగినంత ఒత్తిడి ఉపశమన చికిత్స వెల్డెడ్ ప్రాంతంలో తగినంత ఒత్తిడి ఉపశమనం కలిగిస్తుంది, ఇది సులభంగా పగుళ్లకు దారి తీస్తుంది. హీట్ ట్రీట్మెంట్ లేదా వైబ్రేషన్ ట్రీట్మెంట్ (ప్రధాన కారణం) వంటి వెల్డింగ్ తర్వాత తగిన ఒత్తిడి ఉపశమన చికిత్సను నిర్వహించడం పరిష్కారం.
లిథియం బ్యాటరీల తయారీ ప్రక్రియ విషయానికొస్తే, ఏ ప్రక్రియలు పగుళ్లకు కారణమవుతాయి?
సాధారణంగా, స్థూపాకార ఉక్కు షెల్స్ లేదా అల్యూమినియం షెల్స్ యొక్క సీలింగ్ వెల్డింగ్, స్క్వేర్ అల్యూమినియం షెల్స్ యొక్క సీలింగ్ వెల్డింగ్ మొదలైన సీలింగ్ వెల్డింగ్ సమయంలో పగుళ్లు ఏర్పడే అవకాశం ఉంది. అదనంగా, మాడ్యూల్ ప్యాకేజింగ్ ప్రక్రియలో, ప్రస్తుత కలెక్టర్ యొక్క వెల్డింగ్ కూడా ఎక్కువగా ఉంటుంది. పగుళ్లకు.
వాస్తవానికి, ఈ పగుళ్లను తగ్గించడానికి లేదా తొలగించడానికి మేము ఫిల్లర్ వైర్, ప్రీహీటింగ్ లేదా ఇతర పద్ధతులను కూడా ఉపయోగించవచ్చు.
పోస్ట్ సమయం: సెప్టెంబర్-01-2023